In 2021, the development of China’s aerospace industry is in full swing. Both the construction of the space station and the landing of probes on Mars have achieved great success; more than 50 launches have won the number one in the world and set the country’s annual record. In the field of commercial aerospace, companies such as Deep Blue Aerospace, Zero One Space, and Interstellar Glory have made frequent actions and performed equally eye-catching. 3D printing technology continues to play an important role in this field. In this issue, 3D printing technology reference summarizes the application of 3D printing technology in the aerospace field this year.
1. Zero One Space OS-X6B rocket used 3D printed attitude control power system products to fly for the first time, and the test was a complete success
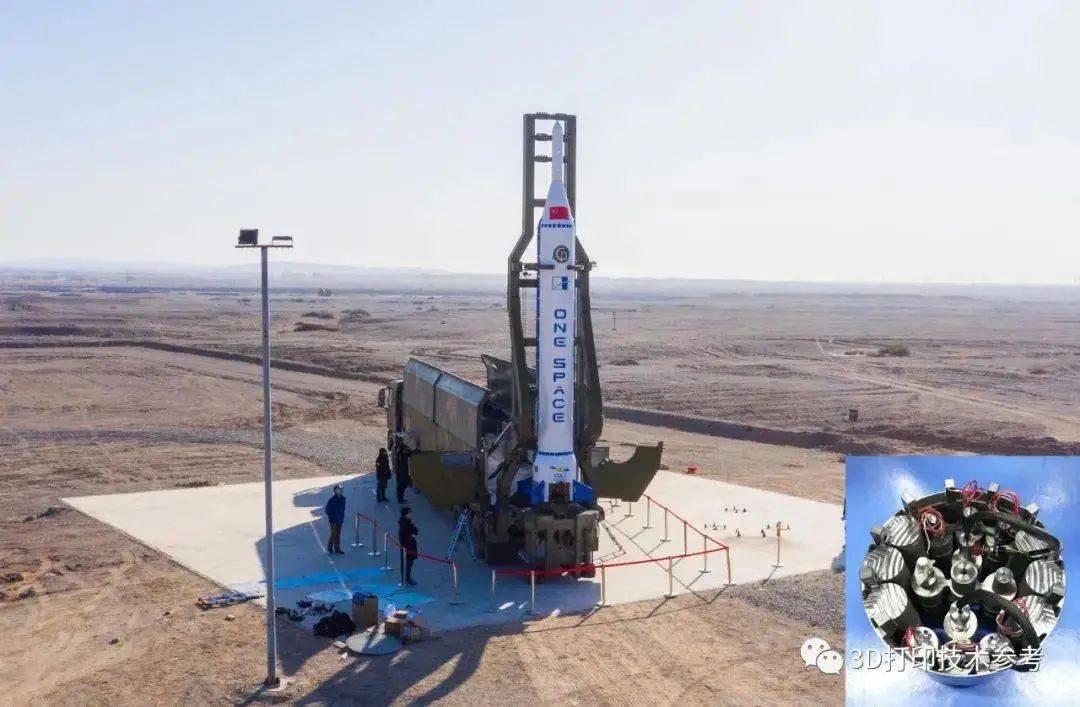
On February 5, 2021, the OS-X6B new intelligent suborbital rocket and “Chongqing Two Rivers Star” independently developed by Zero One Space Technology Group Co., Ltd. were successfully launched at a launch site in the northwest. The test load was successfully separated and the entire flight was normal. The rocket is a zero-one space OS-X series commercial rocket, which is a dedicated flight test platform tailored for aerospace technology verification. The OS-X6B rocket is the first to fly with 3D printed attitude control power system products.
Zero One Space’s self-developed attitude control power system cancels the traditional pipeline to connect various functional components, innovatively applies titanium alloy 3D printing technology, and uses special-shaped gas cylinders as the basis for the integrated design of the system, and prefabricated internal circulation channels in advance to reduce The pipeline components achieve the same function as the traditional pipeline connection scheme, the weight of the whole system is reduced by 34.38%, the mass is no more than 10kg, the reliability of the system structure is greatly improved, and the adaptability is good under the impact of 3000g.
2. Aerospace engine “Yanyu No. 1 A” rocket engine core components are all 3D printing process route
On April 23, 2021, the “Yanyu No. 1 A” liquid oxygen kerosene engine independently developed by Aerospace Engine successfully completed the coordinated hot test, China Aerospace News reported. The thrust chamber, gas generator, etc., the core components of the “Yanyu No. 1” series of engines, all adopt the 3D printing process. The design flexibility is greatly improved, the manufacturing efficiency is significantly improved, and the development cycle and cost of small pumping rocket engines are greatly reduced. .
Compared with the “Rutherford” engine of Rocket Lab’s “Electronics” rocket, the “Yanyu No. 1” series engine saves a lot of components such as batteries and motors, reduces the dead weight of the rocket and the engine, and the engine has a significant specific impulse. Higher than the “Rutherford” engine, it can effectively improve the load capacity of the rocket. At present, there is no mature 2T-level thrust rocket engine in China. This model realizes the full-system verification of a 2T-level liquid oxygen kerosene engine based on the thermal cycle of a gas generator for the first time. Adding a new power spectrum to China’s commercial aerospace field can further promote the cost reduction and technological development of rocket launches, and increase more options for future commercial aerospace and various types of aircraft.
3. Metal 3D printing technology is widely used in the research and development of China’s space station
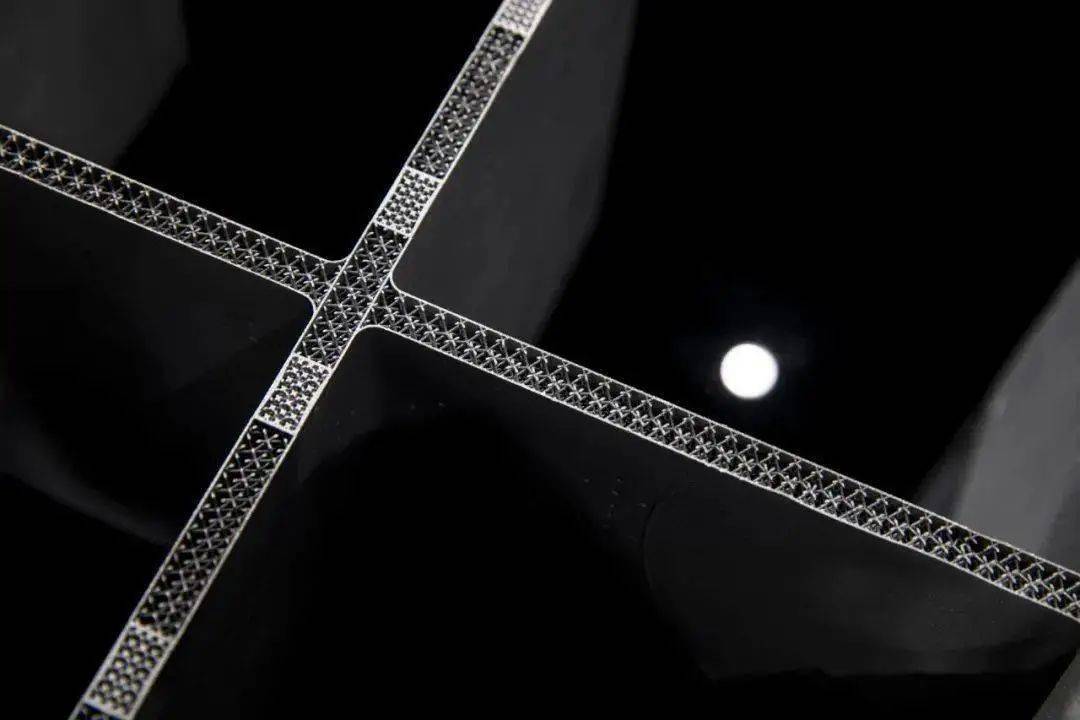
On April 29, 2021, Beijing time, the Chinese space station’s core module “Tianhe” was successfully launched and finally entered the scheduled orbit. According to the plan, the space station’s dream capsule will be launched next year. 3D printing technology reference learned from the China Academy of Space Technology, the important structural part of the Dream Sky cabin uses a 3D printed thin-walled skin lattice structure, and Blite participated in the trial production of the first sample of the component. The designed dot matrix unit is in the form of BCC, the entire guide rail bracket has 11 pieces, and each structural block is integrally formed by BLT-S510, that is, the internal dot matrix structure and the outer skin structure are printed at the same time. The maximum size of a single piece is 400mm ×500mm×400mm, the printing time for a single piece is about 150 hours, and the maximum size of the assembly and splicing part can reach 2000mm after printing.
The skin lattice structure has been maturely used in spacecraft structure products. The 3D printing technology reference also learned in the Chinese Journal of Mechanical Engineering that a closed skin-wrapped equipment support structure with a three-dimensional lattice hierarchical structure designed by the Fifth Aerospace Academy is 46.4% lighter than the structure using traditional design and manufacturing methods. Applied to a certain type of satellite load support mission. The structure of the closed skin wrapping the three-dimensional lattice can effectively improve the design efficiency of the stent structure, and has the prospect of popularization and application in the lightweight of the spacecraft structure.
4. “Tianwen No. 1” and “Zhurong Mars Rover” successfully fall into flames, 3D printing plays an important role
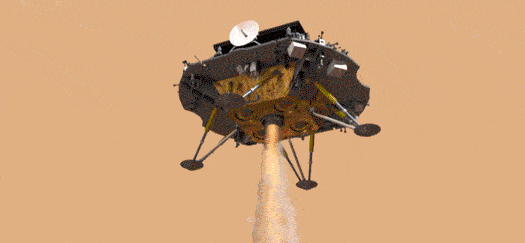
At around 8:20 on May 15, 2021, Beijing time, China’s first Mars probe “Tianwen” successfully landed on the utopian plains of the northern hemisphere of Mars. According to the China Aerospace Science and Technology Corporation, the 529th Factory of the Fifth Aerospace Academy has actively carried out the research and application of 3D printing technology in response to the development needs of the “Chang’e” series, Mars probes and other new-generation lightweight spacecraft, and achieved good results. Researchers from the plant said that compared with traditional castings or forging products, the development cycle of 3D printed products is significantly shorter and the mechanical properties are improved.
On the Tianwen-1 probe, the Sixth Aerospace Academy developed and delivered the propulsion subsystem of the landing patrol and orbiter, with a total of 48 large and small engines. Among them, the 7500N variable thrust engine as the main engine of the landing patrol has achieved important benefits due to the use of 3D printing technology during the manufacturing process: the weight and volume are only one-third of the previous engine, and the structure is more optimized and compact. The docking flange frame of the engine also uses 3D printing technology for the first time, one printing and forming avoids the large margin to remove the deformation caused by the original solid rods or forgings, and also ensures the quality stability of the engine and the overall docking.
5. The Long March 2 F rocket launches the Shenzhou 12 manned spacecraft, and 3D printing makes the rocket engine more reliable
On June 17, the Long March 2 F Yao 12 carrier rocket carried the Shenzhou 12 manned spacecraft carrying three astronauts Nie Haisheng, Liu Boming, and Tang Hongbo into space and checked into the Chinese space station. As the 7103 Factory of the Sixth Academy of Aerospace Science and Technology Group, which produces the core primary engine, secondary engine, and booster engine used in the rocket, 3D printing technology is used to manufacture the required parts, which makes the engine more reliable, and the efficiency and speed are doubled. promote.
The process improvement of the stiffening rib of the engine thrust chamber diaphragm is one of the most typical representatives of the 16 process state changes of the rocket supporting engine. The application of 3D printing technology has realized the “double innovation” of the processing method of strengthened rib products: on the one hand, it has realized the innovation of process manufacturing technology, broke through the traditional manufacturing problems, and solved the problem of low product qualification rate due to structural restrictions; on the other hand; It realizes the innovation of efficient, fast and green manufacturing mode, breaks through the low production efficiency bottleneck of traditional manufacturing mode, solves the environmental protection problems of a variety of waste liquid, dust and smell, and can directly prepare products with complex shapes and stable performance. Compared with traditional castings, the product has higher dimensional accuracy and stability, and a number of product performance indicators are close to or even exceed the historical highest values of traditional castings. Yang Huanqing, director of the Additive Manufacturing Innovation Center of Plant 7103, pointed out that “the use of 3D printing technology to replace the investment casting process has shortened the manufacturing cycle of reinforced ribs by 75%, the pass rate has increased from less than 20% to 98%, and the cost has been reduced by 30%.”
6. Both the Star Glory Hyperbolic II and III rockets use 3D printing technology
According to news from Interstellar Glory in June, the company’s Hyperbolic III liquid carrier rocket has officially shifted from the demonstration stage of the overall plan to the model development stage. The rocket is currently known to be a reusable liquid launch vehicle with the largest diameter, the strongest carrying capacity, and the lowest launch price per kilogram of payload. It will be the main model participating in the commercial launch market launch mission. Hyperbola III adopts a large number of advanced technologies. Among them, the lightweight design technology of the structure improves the efficiency of the rocket structure by adopting 3D printing, composite materials, non-initiated separation, structural integration design, and fine load design. Carrying capacity under the condition of level recovery.
In July, Interstellar Glory announced that the company had conducted ground verification tests for the grid rudder subsystem of the Hyperbolic II reusable launch vehicle. The test process covered the entire process of the rocket mission and achieved complete success. The grid rudder is a kind of rocket flight attitude control device. It is a great technical challenge to design and realize a grid rudder system that can be completely reused on a vertical recovery launch vehicle. The R&D team boldly innovated based on task requirements, and successively completed design and manufacturing difficulties such as multi-scheme comparison optimization, aerodynamic thermal simulation, electrical integration design of structure and mechanism, analysis of adaptability to complex environments, and overall 3D printing.
7. The maximum size is 0.6×0.6×0.6m, and 3D printing deeply affects the manufacturing process of China’s private rocket Deep Blue Aerospace
In July 2021, the Deep Blue Space “Nebula-M” test rocket completed the first vertical take-off and vertical landing free flight test (also known as “Grasshopper Jump”) at the Deep Blue Space Test Base in Tongchuan, Shaanxi. The first flight test mission was a complete success. . The “Nebula-M” test arrow No. 1 is equipped with the “Thunder-5” liquid rocket engine (LT-5) independently developed by Deep Blue Aerospace. It is the first needle-bolt electric pump liquid oxygen kerosene manufactured by using 3D printing technology in China. engine.
The LT-5 engine uses a large number of 3D printing technology, and uses advanced printing equipment to maximize the high strength, ductility, fracture resistance and low variability of the nickel-based superalloy powder material, successfully breaking through the traditional rocket engine manufacturing model The bottleneck of low production efficiency, complicated process route and long cycle. The new engine currently under development also chooses the proven 3D printing technology and post-processing technology, and the maximum size of the newly delivered engine structural components reaches 0.6×0.6×0.6m. Through a series of research and development tests, we have independently mastered many key technologies such as 3D printing powder selection, additive manufacturing shape control, and high-quality abrasive flow finishing on the surface of the additive runner structure. The product has multiple rows and multiple cavities. , Regenerative cooling channel and other complex and precise components of additive manufacturing capabilities.
8. The Second Academy of Aerospace Science and Technology of China used 3D printing technology to achieve important milestones in aircraft development
On August 27, the Second Department of the Second Academy of Aerospace Science and Technology of China announced that it has realized the 3D printing integrated manufacturing of the complex structure of a certain type of aircraft product, and pointed out that this is an important milestone in the development of 3D printing technology in the aerospace field. The lightweight level of aircraft provides strong support for the development of a new generation of aircraft in the future.
The Second Department of the Second Academy is China’s earliest unit engaged in cutting-edge science and technology and research and development, and is China’s most important missile weapon system research and production unit and a leader in the development of air and space defense. According to the experts of the second department, the aerospace vehicle product has many structural parts, long production cycle and high cost. The “mouldless” manufacturing of aircraft structural products doubles the production efficiency. On the basis of ensuring that the performance does not drop, the cost is reduced by nearly half, which solves the problems of long processing time, difficult quality control, and high cost in the traditional production mode. 3D printing integrated molding technology, digital manufacturing capabilities have been greatly improved.
9. Xingzhong Space “Smart” space experimental satellite is manufactured by 3D printing
On December 17, the “Smart” space experimental satellite printed by Blite and produced by Xingzhong Space carried the “Huayi-1” suborbital rocket launched by Shaanxi’s first commercial rocket company, Shaanxi Huayi Hongda Technology. The first flight was successfully carried out at a proving ground in Northwest China.
3D printing technology reference learned that the metal 3D printed “Smart” satellite is a satellite platform specially designed for biology, medicine, materials, energy and other space experiments. Bright was responsible for the printing of the main frame structure of the “Smart” satellite this time, including 4 panels and 4 beams. In order to meet the technical requirements of light weight and high rigidity of the main frame structure and the urgent node requirements of the project, Blite uses AlMgSc high-strength aluminum alloy as the raw material and the BLT-S400 three laser equipment to achieve rapid development. Blite responded quickly after receiving the production task, using the BLT-S400 series three-laser equipment to complete the forming in one furnace, and the switchboard time was 35 hours. Due to the urgency of the project, the parts are internally circulated for 24 hours, and after post-processing, machining, anodization, etc., the delivery will be completed at 10 pm on the deadline. The total project cycle is 8 days.
10. The 211 Plant of the First Academy of Aerospace Science and Technology successfully mastered the 3D printing technology of high-strength aluminum alloy cabin
According to China Aerospace Science and Technology Corporation, the 211 Plant of the First Academy of Aerospace Science and Technology successfully mastered the 3D printing technology of high-strength aluminum alloy cabin in 2021. High-strength aluminum alloy cabins are commonly used in multiple models of products from the 211 factory. In the past, the products of this type of cabin section were mainly cast and forged, but there were “defects” in the production of casting and forging. In the pre-research stage of a key model, the factory proposed to adopt an additive manufacturing method, which was approved by the design department.
However, the rough weight of the cabin section is too large, which exceeds the load-bearing limit of the working platform of the arc additive equipment. The research team independently researched the structure of the working platform, removed the waste weight of the platform, and designed and manufactured the “eight claw” structure tooling, which not only greatly reduced the weight of the platform, but also maximized the size of the formed parts. However, as soon as the cabin section was put on the shelf, the problem reappeared. Due to the characteristic structure on the inner wall, the cabin section needs to be turned 90 degrees and then formed. However, the cabin section is too heavy, and the turning is susceptible to inertia, resulting in a position shift. The research team designed a positioning and card installation plan without increasing the weight, which solved the problem of cabin offset in the printing process. The factory successfully mastered the 3D printing technology of cabin products.